NOMADOMO
BlogDismountable, fireproof, and "eatable" buildings and boats.
Nomadomo blog 2019
I want to make liftable buildings. December 2019 this website went online. This section of the website deals with time-ordered matters, such as changes to this website, and new thoughts and events. Have fun! [Bert Frederiks]
2019 -12-29: Sheet material: OSB, plastic, wear, microplastic
Plastic (in the sense of polymers) and additives to it eventually always partly leak into our environment and into ourselves. Glue is (almost always) also a plastic. When we breathe in plastic in the form of nanoparticles they are poisonous. Rub with your shoulders along an OSB plate (also the so-called "ecological" variant) and you rub plastic into the air. If you cut wooden plates, the plastic in them will (partly) blow into the world. The sun turns them into nanoplastics and so you breathe them in or something or someone eventually eats them.
The world is already so full of plastic that it seems almost pointless to worry about it. But if our idea is going to conquer the world and reduce concrete and energy consumption, we shouldn't put more plastic into circulation instead.
Until recently I still had the idea that polyethylene foil sheltered from the sun was OK enough because it wouldn't decay, but after some conversations with a chemist friend, I know that's not true. It also decays without sunlight, but more slowly. As such the durability of houses with plastic can be questioned. If the houses from the Dutch Golden Age would have been built with plastic, they wouldn't be there any more. Yet plastic remains in our environment for hundreds of years.
There are some wooden plate materials without (oil-based) plastics. They are little or not suitable for structural use, but otherwise fine. One problem is that the fire class is often "E", while in the Netherlands "D" - for a wall as a whole - is required. The only positive exception for structural use I thought to have found is "Pavaplan 3F", but it seems to contain glue: Phenol or PVA or PUR? By the way, there is one type of glue that I think is OK: PVA or Poly-vinyl acetate. In order to make fibreboards water resistant, there might be bitumen on them, which I also have my doubts about.
As far as wood boards are concerned, it is personaly striking to me that they often contain additives to which I am allergic. Unfortunately, I am also allergic to rosin and therefore to spruce, but that is only important when sawing and sanding.
Plates based on straw, hemp and the like are almost always glued. For what it's worth it is really formaldehyde-free because wood also contains formaldehyde and fumes this out - with OSB-zero I think this is wrapped in the plastic in such a way that it doesn't come out.
There is some kind of exception...: CANAPAlithos® from CMF Greentech. They use a mysterious binder. I finally found their patent and it is not plastic! It is based on magnesium oxide and sulphide with the help of soy bean starch. So it is a kind of cement. The plate is quite strong; only a few times less strong than wood and OSB. To what extent you can use it structurally without extensive testing I don't know.
There may be some kind of exception, if we may believe the marketing...: Resysta, made from rice waste (60%), salt (22%) and mineral oil (18%). It can withstand almost anything and is non-combustible but still a thermoplast: You can deform it at 120 degrees or melt it together! You just don't have to try to burn it, so recycle it. But you can't use it constructively: no CE marking. Or is this plastic? There is also vinyl polymer in it!? After a long search I found out that through a "PTRH technology" (?) the rice husks are converted into plastic. So still plastic:-(
Plates based on concrete (fibre cement), loam, gypsum, magnesium oxide or calcium silicate, are often not constructively applicable. But with the addition of wood fibres, for example, this does exist: Cembrit, Eternit, Fermacell, Permoxx, Promat, and Siniat.
Clay slabs with certain fire resistance are also for sale, for example from Lemix, but cannot be used constructively.
It would be so nice if I could just use HDPE pallet boxes for the floor bins... They are often made of recycled plastic. Some people think that by recycling you help to take the plastic out of the world…
2019 -12-14: Old drawing of an angled wall: intermediate frame
2019-12-10 I wrote that supporting beams would have to go through the inner wall to get them into the fire protection. However, not so long ago, before I started working on my theory, I solved it very differently: see drawing. I then let the fire resistant side plates extend to the vertical inner wall, with a vertical linking beam between the wall sections.
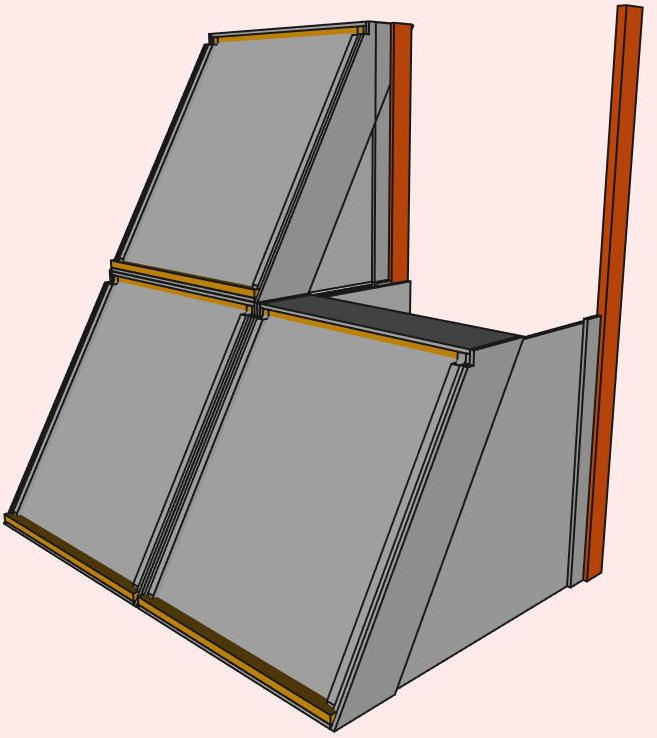
The linking beam could also be made half as thick and pre-mounted on the sideboard. Then you get an intermediate frame.
A disadvantage seems to be that you have to screw through the fire resistant plate, but that may only be necessary at the ends. It depends on how well everything has to stay in place during a fire.
In this construction maybe you hardly need beams in the walls? If you allow plates to overlap, you already get a considerable thickness and strength. In addition, normally your wood needs to be extra sized for when it burns away. This is less necessary with other materials.
In terms of stiffness and a self-supporting frame, the wall may not be as effective. These forces are largely applied to the plates of the wall. Linking beams or an external linking skeleton must be able to transmit these sufficiently.
So I have to add another chapter to my theory…
2019 -12-12: An overgrown, compostable house that stands for 100 years
I have an image in my mind of a house that looks like a wet, overgrown rock..., a kind of living, hollow stone, that preserves rainwater and pumps around. But at the same time the house has to be liftable and ecologically sound, thus not made of plastic. Then everything that is not compostable is made from stone, glass, concrete, ceramics or sand... Composting starts with moisture, so when it's wet...
Stone, glass, concrete and ceramics are not light-weight, but they exist in the form of thin sheets or tiles. I think plastic foil under sand is acceptable. Metals may be an option, but zinc and chrome are poisonous in many ways, so their use is not trivial.
Interesting materials are all kinds of stucco. Nowadays this seems to be made of concrete mostly. A pity is that with these products you never know exactly what you are buying. In concrete can be all kinds of heavy metals.
Ceramics exists all forms of tiles. Usually tiles themselves make the roof waterproof. But you can also use ceramics to only protect underlying plastic foil against the sun and mechanical wear by rain. You can install tiles or slates such that the roof is waterproof, but you need much less of them if you let plastic foil do that.
There are climbing plants that are so proliferating that they could completely cover plastic foil. I don't know how well this goes together with growing vegetables?
A nice colour for roof tiles would be purple. Plants do not grow on green light. I think it works like this: Green is the colour of the leaves themselves and green light is therefore converted into heat. Red and blue (thus purple) light can be used for photosynthesis, so if you reflect that from the house... White light is also good, of course, but that's a bit boring.
2019 -12-10: Angled walls
Because I want as much plants and vegetables on my buildings as possible, I'm now trying to draw a stepped wall. A concrete problem with a real stair-shape is that higher wall sections are placed somewhere in the middle of a part underneath, and that is usually not the strongest spot. Also in terms of fire safety it's not right because this is outside the fire-resistant area.
I have always drawn sloping walls, and now I remember why. In my first drawings I then made a box at the underside of the roofing that was 30 centimetres wide and deep - as if you were bending a corrugated sheet on the underside both 30 centimetres to the outside and upwards.
I think you can do this with all kinds of materials, even wood. On a roof with a slope of 60 degrees you make a plank with a slope of 30 (which is perpendicular) to 60 degrees the other way around. Inside you can put polyethylene foil, with drainage to the sides. At the connection of the wall sections should be a gutter for drainage.
Preferably, the water is also collected. Place a plank at the bottom to create a double floor. Then you can drain the water at the bottom, but also collect it in there. Water that flows from the roof can be made to run into the planter, but it can also run directly into the gutter underneath.
2019 -12-08: Linking skeleton
Now that the foundations are online I thought I could finally start drawing, but I soon came up with a new option. So the creation-analysis circle is far from over - of course never comes to the end, but...
One of the complications with linking beams is that, especially if you want to use them both inside and outside, the thickness of the wall sections is quite tight. However, if, instead of a complete inner or outer frame, you only mount the horizontal or vertical beams, then you can lay the linking beams on these. This comes much less tight than mounting them on the outside.
If you only mount the horizontal or vertical beams, then you can also easily connect without link beams. The skeleton itself becomes sort of a link beam. So you get a kind of Linking skeleton.
Take a horizontal beam at the bottom of a wall section. You can now screw it to a floor box at the ends. This is not possible if there is an equally thick vertical beam above it. A thinner vertical beam would be fine. The horizontal beam can then look like a skirting board. The difference with a link beam is that it does not connect multiple wall elements itself.
Take only vertical beams - a vertical linking skeleton. Now you connect the wall element to the floor with a small link beam or connecting plate.